Digital solutions
Digital solutions are used wherever the collection, transmission, processing and analysis of relevant information in intralogistics is required. The aim is to support our customers during the planning phase so that the right information is available at the right time and in the right place.
Such digital solutions can also be networked forklift control systems, warehouse management software or fleet management solutions, for example.
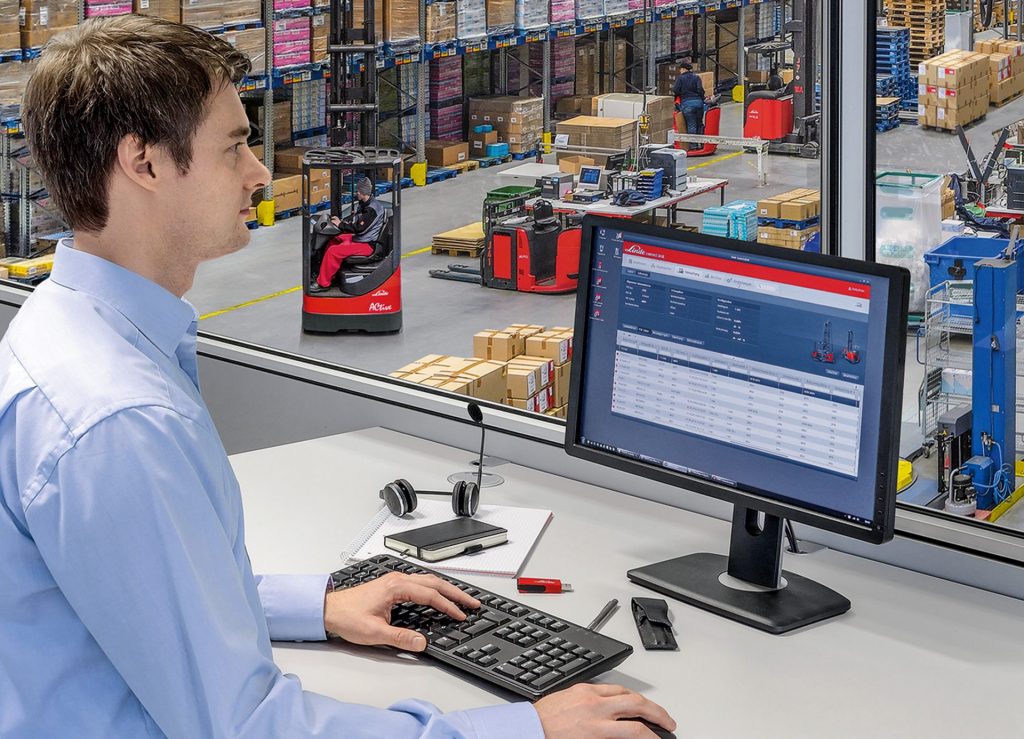
Your digital fleet management
Digitalisation is changing the world of logistics. With the growing amount of data and networking in the industry, logistical processes are becoming increasingly complex. Vehicles act partly autonomously and communicate thanks to numerous sensors – the fleet is becoming intelligent. Fleet managers control processes in real time and achieve significant increases in the turnover of goods.
The Linde connect fleet management system provides precisely the information that fleet operators need to use their vehicles efficiently – regardless of location and fleet size, new and existing vehicles or equipment from other manufacturers.
Linde connect – The way to your smart fleet
The Linde connect product family networks vehicles and continuously informs fleet managers about the status of their logistics in production or warehouses. This transparency makes the use of a fleet safer and more economical. Digital solutions thus increase the availability of each individual vehicle.
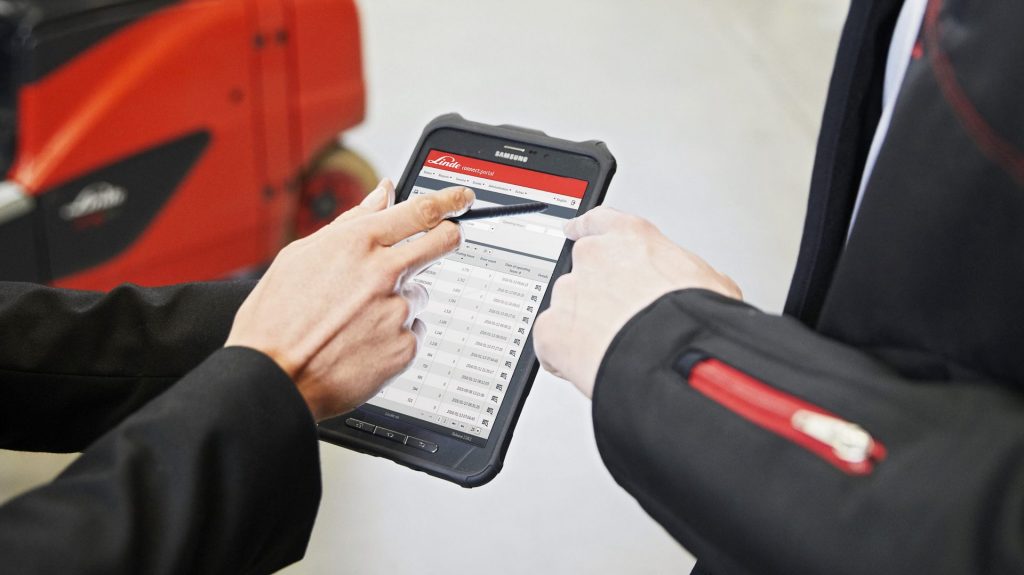
More efficiency through digital solutions
- Identification of under-utilised and overloaded vehicles
- Recognition of fault-prone vehicles
- Improvement of the logistics processes
- Increase vehicle availability
- Identify and document bottlenecks at an early stage
- Identify and reduce or avoid overcapacities
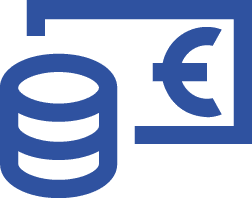
Highest security through digital solutions
- Exclude unauthorised use of vehicles
- Limit wilful misuse and rough driving behaviour
- Eliminate hazard hotspots
- Automated speed adjustment in zones
- Recognise restrictions on the vehicle at an early stage
- Increase sense of responsibility
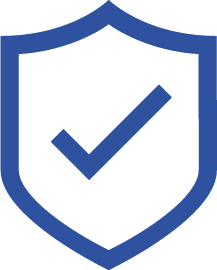
More transparency through digital solutions
- Clear assignment of drivers and vehicles
- Managing driving licences, training and more
- Mapping the organisational structure in fleet management
- detailed usage and consumption data
- Individually configurable, meaningful reports
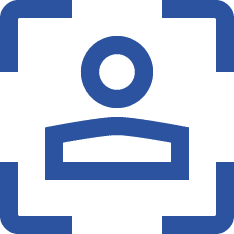
Optimal service through digital solutions
- Reduce violence damage
- Keeping track of maintenance intervals
- Avoid overloading individual vehicles
- Stemming key loss
- Detect damage to the vehicle at an early stage

Functions of Linde Connect
The requirements for a fleet management system are often very specific: every company offers a different operating environment for the industrial trucks in a fleet. Accordingly, the individual functional modules of Linde connect can be combined individually to create a system that optimally meets the respective requirements.
With connect:ac, operators control access to their fleet: who is currently at the wheel of which vehicle? connect:ac creates the basis for planned fleet deployment.
access control – The electronic key
With connect:ac access control, you control access to your fleet. The application allows you to unlock the vehicle via PIN or RFID, assign drivers and vehicles and manage authorisations (for example driving licence or and eye test).
- Unauthorised use of vehicles no longer possible
- Access controllable by person, validity period, driving authorisation and vehicle
- Proof of vehicle use possible at any time
- Driver-specific vehicle settings, for example reduction of speed
- Key loss is no longer possible
- More conscious handling of the vehicles by the drivers
- Contactless identification by RFID transponder or PIN procedure via number field
- Also available as retrofit solution
Pre-Operational Check – Pre-Shift Check per App
The app for smartphone or tablet ensures a safe and simple vehicle check before each assignment. Defects can be documented immediately by photo and transferred to the fleet manager. The vehicle can only be started when the check has been carried out and the vehicle is ready for use.
- High operational safety, as the vehicle can only be started after a successful pre-shift check
- Simplified pre-shift check via app with immediate added value
- Regular enquiry about the condition of the vehicle
- Digitisation of examination results saves paper
- automatic e-mail report in real time
- Photo documentation of the damage or conspicuous features on the vehicle
- Questions freely definable by the fleet manager via a configurator
- Documentation of all defined questions and answers
- App for all Android mobile devices with NFC technology
- Also available as retrofit solution
connect:dt documents the use of fleet vehicles: Was a vehicle in operation a lot or was it often stationary? Were there any accidents? Is the vehicle in working order?
crash detection – electronic damage monitoring
Has there been an accident? Is any part of the premises uneven? Is a driver driving carelessly? With connect:dt crash detection, the time and strength of strong vibrations that can cause damage to the vehicle are recorded.
- Identification of danger spots or soil damage on the company premises
- wilful misuse or gross driving behaviour is attributable to individual drivers
- Reduction of damage due to improper treatment
- Reduction of repair costs
- Early detection of damage to the vehicle
- Automatic speed reduction of the vehicle adjustable
- Recording threshold individually adjustable
- Identifying the driver in the event of accidents or damage to buildings
- More conscious handling of the vehicles by the drivers
- More safety on the company premises
- Also available as retrofit solution
With connect:an, fleet managers analyse and monitor the performance of their fleet: How often does a vehicle drive or lift? How much energy does it consume?
usage analyses – The digital benefit analysis
How are the shares of driving and lifting distributed when using a vehicle? Does the usage correspond to the performance profile of the vehicle? connect:an usage analysis provides details on how well the vehicles and the entire fleet are utilised.
- Overview of the availability of the vehicles
- shows the actual fleet performance
- Easy identification of underutilised vehicles
- Makes potential for improvement within the fleet visible
- Reduces new purchases or the use of replacement vehicles
- Transparency about fleet deployment
- Enables conclusions to be drawn about the behaviour of individual drivers
- Data transmission possible via various communication technologies
battery management – The digital battery care
Is the battery properly maintained? Are batteries often charged too early or too late? connect:an battery management uses recorded parameters to evaluate the condition of the battery and detects possible operating errors.
- Avoidance of damage and loss of performance due to incorrect loading or maintenance
- Increase in vehicle availability
- Avoid unnecessary maintenance or replacement costs
- Battery parameters transparent at a glance
- Notification when limit values are reached
- Energy consumption clearly quantifiable
- Operating errors can be assigned to drivers
- Identification of infrequently used or overused batteries
- Raising awareness of drivers in the area of energy management
Hardware components from Linde-Connect
The hardware components of Linde connect link vehicle fleets with software databases. They collect and transfer control and sensor data and make it available for further processing. Alternatively, they serve as an electronic ignition lock with PIN or RFID identification.
New vehicles are delivered ex works with the Linde connect hardware, but all components are also available as retrofit solutions for existing and third-party vehicles. Linde offers data communication via GPRS to the Linde Cloud and Bluetooth to local databases as standard. Other wireless transmission technologies such as WLAN can be implemented as customer-specific solutions.
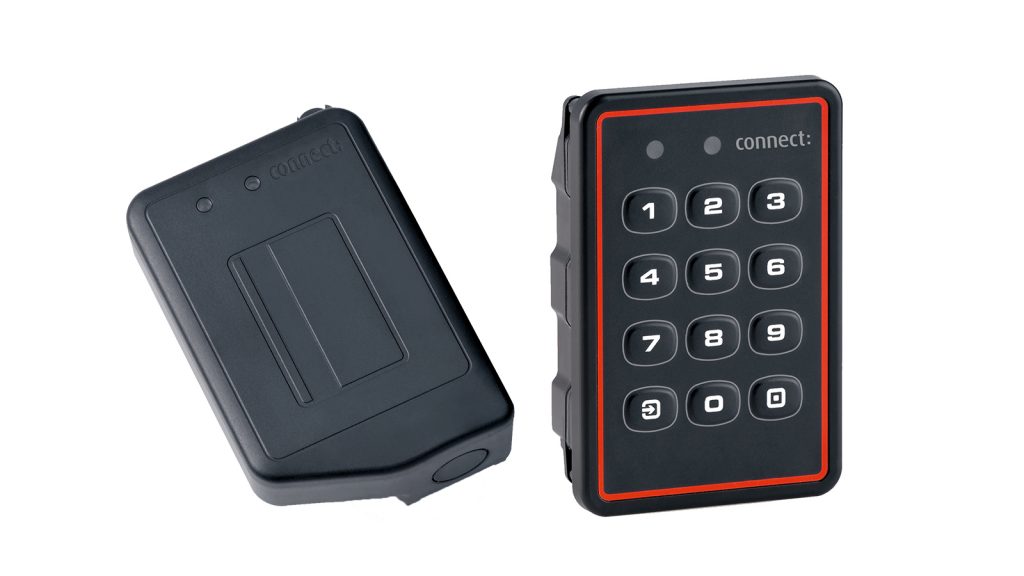
Only authorised drivers can unlock and use the vehicle via the connect:access units using a PIN or RFID chip. The software for additional connect: function modules can be uploaded via the Bluetooth connection. Both the PIN and RFID units can be retrofitted to existing vehicles from Linde or other manufacturers without any effort.
The CDX unit records data on the vehicle and transmits it to the Linde Cloud servers via the mobile network. It can be ordered as a complete retrofit kit from Linde’s global spare parts warehouse in Kahl. The assembly of the components takes only a few minutes. The unit is connected to the CAN bus and is immediately ready for operation after installation.
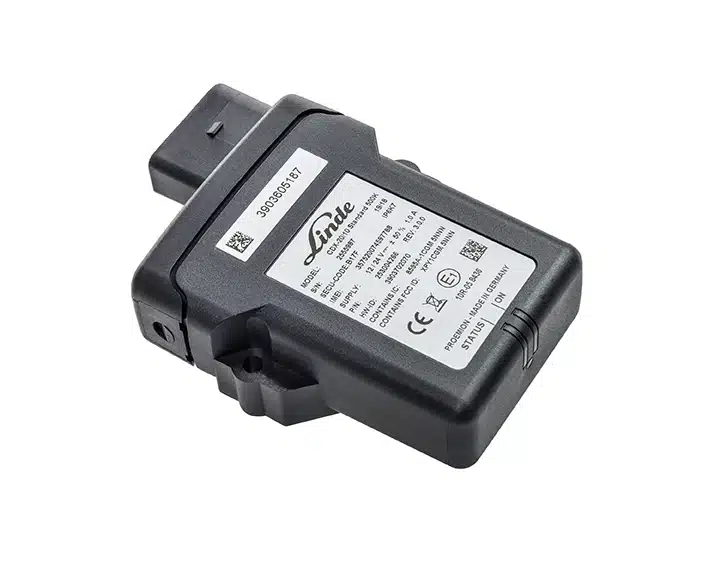
Software from Linde Connect
The connect: software offers you clear access to all your fleet data. It is used to manage vehicle and driver data and allows you to easily compile reports.
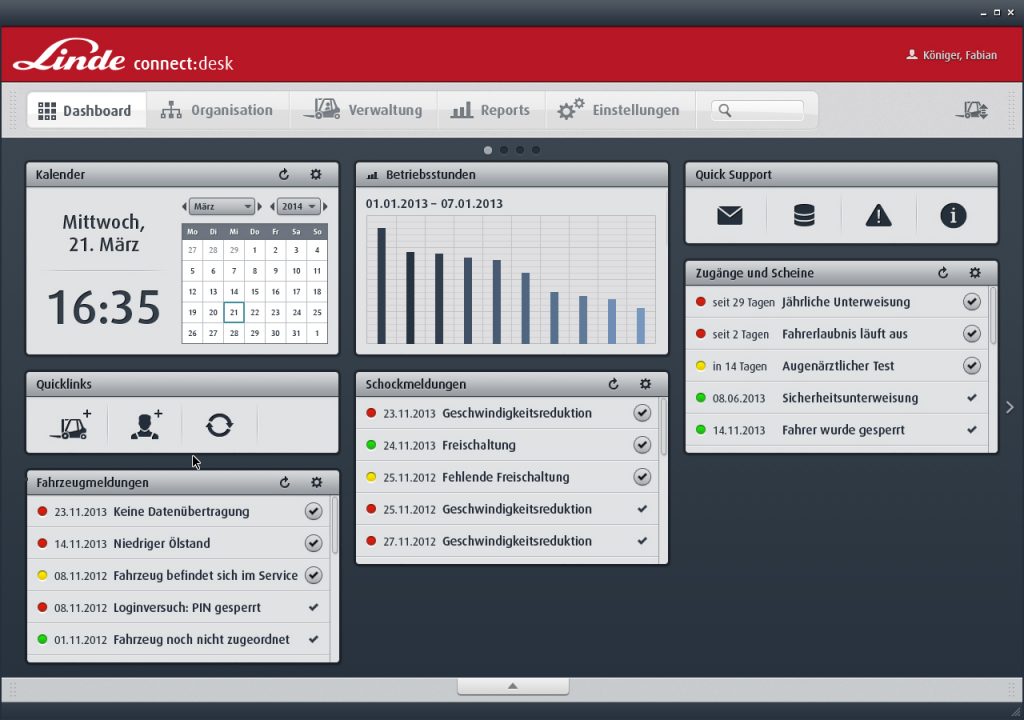
CONNECT:DESK –
The fleet management software
From the management of vehicles and drivers to fleet deployment planning, monitoring and analysis of vehicle data to maintenance planning – connect:desk is the centrepiece for the entire fleet management. The software is suitable for both experienced fleet managers and occasional users who only need individual functions.
Bluetooth, WLAN or mobile radio – the optimal transmission technology is available for every infrastructure and fleet. All three variants run automatically in the background without the driver or fleet manager having to actively contribute anything. The transmissions can also be combined within a fleet.
Within the WLAN network, the data is transmitted directly from the vehicle to the database.
- Data security: The data does not leave the company. The user therefore has complete control.
- No new infrastructure required: connect: uses the existing WLAN network in the company.
- Up-to-date data: Due to the wide-area coverage, the data is transmitted promptly and is available very up-to-date in the connect:desk.
- Authentication algorithms and IT standards: Authentication via WPA2 (with password) or WPA2- Enterprise (certificates) complies with standards and is secure.
- The vehicle must be equipped with a WLAN box, available as a retrofit kit.
- Experts from connect: take over the one-off commissioning on site.
- For the implementation of WLAN transmission, cooperation with the company’s IT department is required.
The data is sent to the database via the mobile network.
- No infrastructure required: Unlike Bluetooth or WLAN, no hardware is needed on the premises to transmit the data.
- Indoor and outdoor: The vehicles can transmit data indoors and outdoors. The stability of the connection depends on the network of the mobile phone provider.
- Quick and easy installation: The data unit can be retrofitted to older vehicles in a few simple steps.
- The online box can be ordered ex works for almost all new vehicles.
- For older vehicles, there are retrofit kits for many model series that can be installed in just a few steps.
- No additional infrastructure, such as SyncPoints or WLAN hotspots, is required for data transmission.
Reports and analyses
Based on the comprehensive data on the vehicle fleet, more than 15 interactive reports on the fleet, individual areas, vehicles or drivers can be called up with the connect:desk software. The data is presented in clear diagrams and tables. This way, fleet managers know exactly which vehicle was used when, by whom and how.
- Logbook: List of all recorded events of individual vehicles
- Usage: Overview of the use and utilisation of all vehicles
- Service: Service and maintenance dates for all vehicles at a glance
- Coordination: Overview of the use and utilisation of all vehicles
Overview of the most important reports
Here you can see who has used which vehicle at what time. The login and logout times of the driver are recorded for each vehicle. Special events or accidents can always be clearly assigned.
With the help of the shock values, you can understand when a driver has caused a shock to the vehicle – for example through a collision or a pothole. This increases the drivers’ sense of responsibility.
Here you will find detailed information about how a vehicle is used: How long is a driver registered? How is this time divided between driving and lifting?
You receive an overview of all upcoming maintenance and service dates for the vehicles in your fleet. This makes scheduling easier. In addition, you can bundle maintenance appointments in this way and thus reduce your costs.
This report helps you optimise the vehicle fleet. Here you can see how long vehicles are used or whether they are perhaps not used at all. The evaluation is possible for the entire fleet or for individual vehicles.
Here you can see at a glance how your fleet is made up – broken down by manufacturer, vehicle type and other criteria.
We are happy to advise you
Digital solutions are always used where the collection, transmission, processing and analysis of relevant information in intralogistics is involved. Let our experts advise you comprehensively.
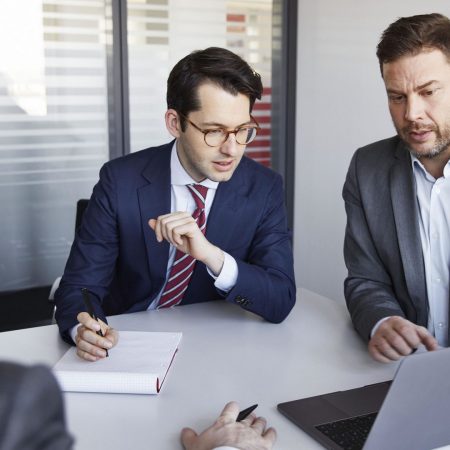